Contexte
L’automatisation des entrepôts demeure un sujet de débats au sein du secteur de la grande distribution. Entre les innovateurs qui embrassent les projets automatisés les plus ambitieux et les conservateurs qui optimisent toujours plus les méthodes conventionnelles, le fossé se creuse. Dans un secteur caractérisé par des marges étroites et des volumes massifs et prévisibles, les investissements considérables ne sont envisageables que si le Retour sur Investissement (ROI) est assuré. Au cours de la décennie écoulée, des entrepôts remarquables ont émergé, notamment à l’initiative d’E. Leclerc et d’Intermarché.
Aujourd’hui, de nouvelles contraintes comme la pénurie de main-d’œuvre ou encore le coût du foncier ont rendu l’automatisation quasiment incontournable pour les grandes enseignes, au moins pour une partie des références traitées.
La plupart des enseignes de grande distribution se sont ainsi lancées dans l’automatisation de leur entrepôt “sec” (c’est-à-dire pour les produits conservés à température ambiante).
L’objectif est double
Accroître la densité de stockage pour réduire l’impact sur la surface au sol, et améliorer la performance lors de la préparation des commandes.
En parallèle, l’accent est mis sur l’amélioration de la qualité de service, avec la minimisation des erreurs et la simplification de la mise en rayon dans les hypers et magasins clients. De plus, une réduction de la pénibilité est visée pour les préparateurs de commandes.
Forte de résultats encourageants, la grande distribution se penche aujourd’hui sur l’automatisation des entrepôts “frais”. Les objectifs restent identiques, mais les enjeux diffèrent. Par la nature de ces produits ayant une date limite [ Date Limite de Consommation (DLC) ou Date Limite d’Utilisation Optimale (DLUO) ] courte, les entrepôts frais fonctionnent en flux tendu afin de limiter la perte en magasin. Les produits réceptionnés à la centrale sont donc expédiés dans la journée.
Ce flux se décompose en :
Réceptions, préparations et expéditions, sans aucun stockage à l’exception des stocks tampons nécessaires au séquencement des articles et à la constitution des palettes « filles » (à destination des clients).
Pour traiter les produits frais, certains entrepôts s’équipent depuis longtemps de trieurs horizontaux, permettant d’accroître la productivité et de sécuriser la préparation. Mais cette approche présente des limites (voir ci-dessous), ce qui a conduit certaines plateformes, comme celle de la SOCAMIL près de Toulouse, à s’équiper d’un système entièrement automatisé de l’équipementier WITRON. Face à ces approches radicalement différentes, les grandes enseignes se posent aujourd’hui la question de la solution la plus adaptée à leur fonctionnement.
Leurs engagements :
Livraison en temps et en heure
Les magasins ont la contrainte du temps pour la mise en rayon des produits. Généralement, les livraisons vers les magasins s’effectuent entre 5h et 6h30 et la mise en rayon doit prendre fin avant l’ouverture.
Respect des commandes
La commande livrée est identique à celle commandée (pas d’inversion de produits ou produits manquants pour ne pas engendrer de rupture en magasin).
Répartition des produits par famille
Cette construction spécifique des palettes permet d’optimiser la mise en rayon par le personnel des magasins.
Qualité des produits livrés
Le « tétris » de palettisation doit garantir l’absence de casse ou de dégradation des produits.
Le trieur
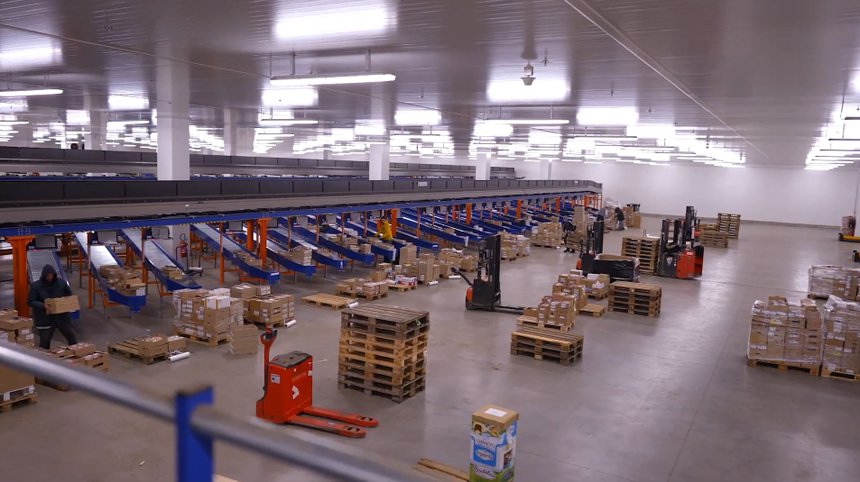
L’introduction du trieur a été motivée par la nécessité de répondre efficacement aux exigences des processus de flux tendu. Ce dispositif est particulièrement prisé dans les domaines de la messagerie et de la distribution en raison de sa capacité à assurer un tri performant des produits. Il s’est imposé comme une solution éprouvée dans les entrepôts frigorifiques de la grande distribution, en réussissant à répondre de manière optimale aux contraintes du flux tendu et en triant un volume maximal de produits dans un laps de temps limité.
Les trieurs les plus performants peuvent traiter jusqu’à 20 000 colis/heure tout en maintenant la qualité dans la préparation des commandes, grâce aux tunnels de lecture réguliers permettant d’identifier ou de contrôler les produits injectés.
Ces systèmes de tri à haute cadence, malgré leur prix élevé, offre généralement un retour sur investissement rapide. Ils ne résolvent cependant pas tous les problèmes des entrepôts frais.
En effet, de nombreuses enseignes ont du mal à recruter ou fidéliser leurs employés. Les entrepôts gagnent en productivité grâce aux trieurs, mais très peu sur le volet de la pénibilité : les préparateurs continuent de manipuler la totalité des produits, la charge portée par jour et par préparateur se chiffrant parfois en tonnes, ce qui va évidemment à l’encontre des recommandations des Caisse Régionale d’Assurance Maladie (CRAM). Les intégrateurs de ces solutions cherchent à résoudre le problème avec des postes ergonomiques d’injection et de palettisation, mais cela reste insuffisant.
Il est complexe d’optimiser la palettisation en sortie d’un trieur. En effet, les produits arrivent en fonction des injections : la répartition optimale des poids n’est donc pas réalisable et des produits lourds se retrouvent au-dessus de produits légers. Cela impacte nécessairement la qualité des produits et palettes expédiées.
En conclusion, bien que le trieur puisse constituer une réponse aux exigences de ces entrepôts, il demeure dépendant d’une main-d’œuvre conséquente, dont le recrutement devient de plus en plus complexe. D’autre part, il ne répond pas entièrement aux exigences de qualité et de niveau de service attendues.
Avantages
- Investissement
- Erreurs de préparation limitées
- ROI rapide
- Implantation rapide
Inconvénients
- Main d'œuvre encore conséquente
- Pénibilité des manutentions
- Qualité de palettisation dépendante de l'ordre d'injection des références
Une solution plus automatisée
Avec la réussite des entrepôts secs entièrement automatisés, les grandes enseignes se tournent vers des process similaires pour les entrepôts frais.
Pour répondre aux demandes de leurs clients, les intégrateurs ont réalisé de nombreux développements sur leurs solutions afin de les adapter aux contraintes d’un flux tendu.
Voici le schéma des flux d’une solution avec un buffer automatisé :
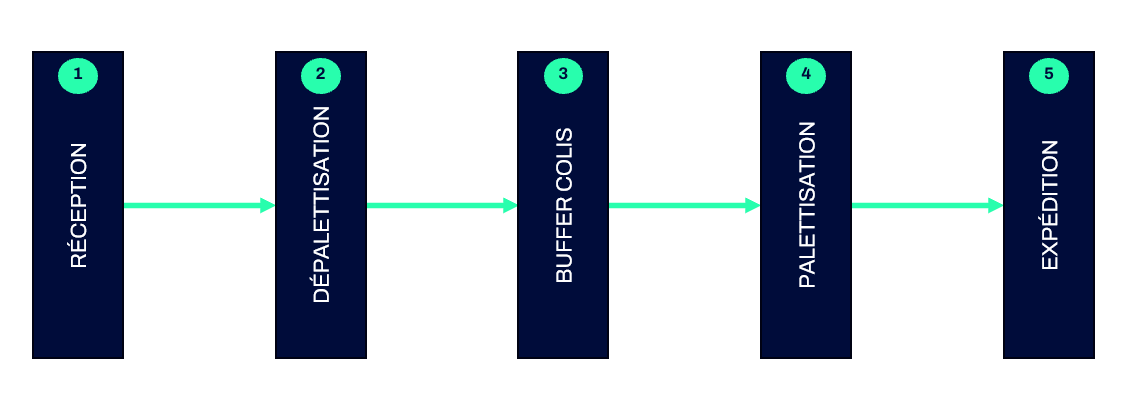
1. Réception
Les caristes déchargent les camions et trient les palettes en fonction des familles de produits et de la typologie des palettes (dépalettisation automatique ou manuelle). Ils injectent ensuite les palettes dans le système.
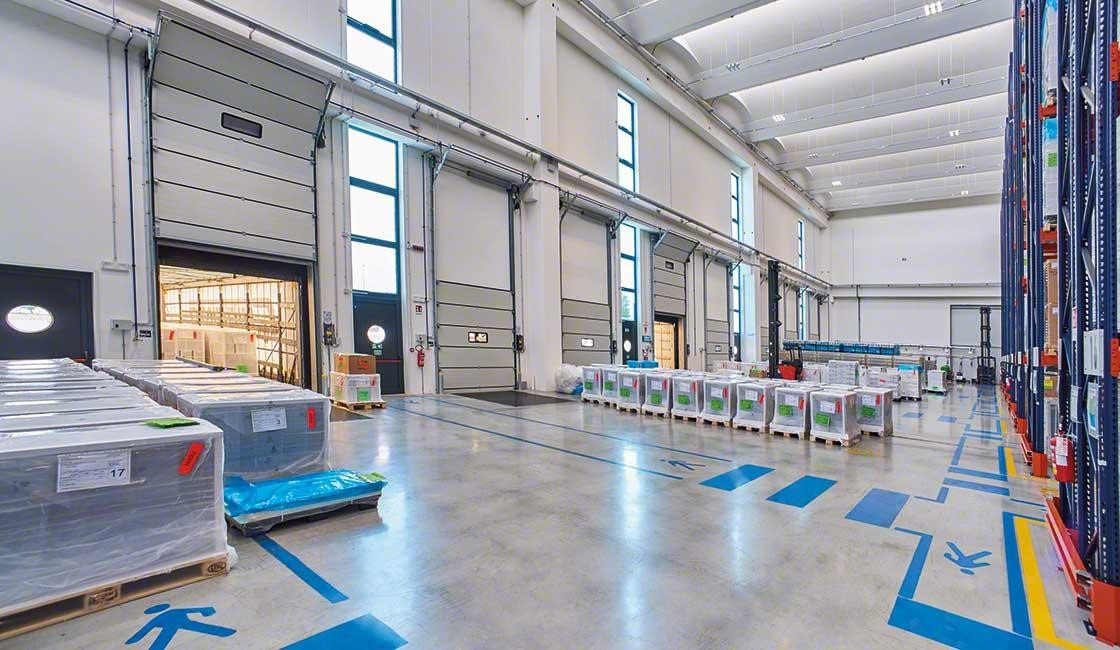
2. Dépalettisation
Il y a deux technologies pour la dépalettisation (automatique et manuelle). L’automatique est aussi performante que 3 postes manuels.
Attention : certaines familles n’ont pas la même proportion de volumes dépalettisables en automatique. Les lignes de dépalettisation auto doivent pouvoir être temporairement utilisées en manuel.
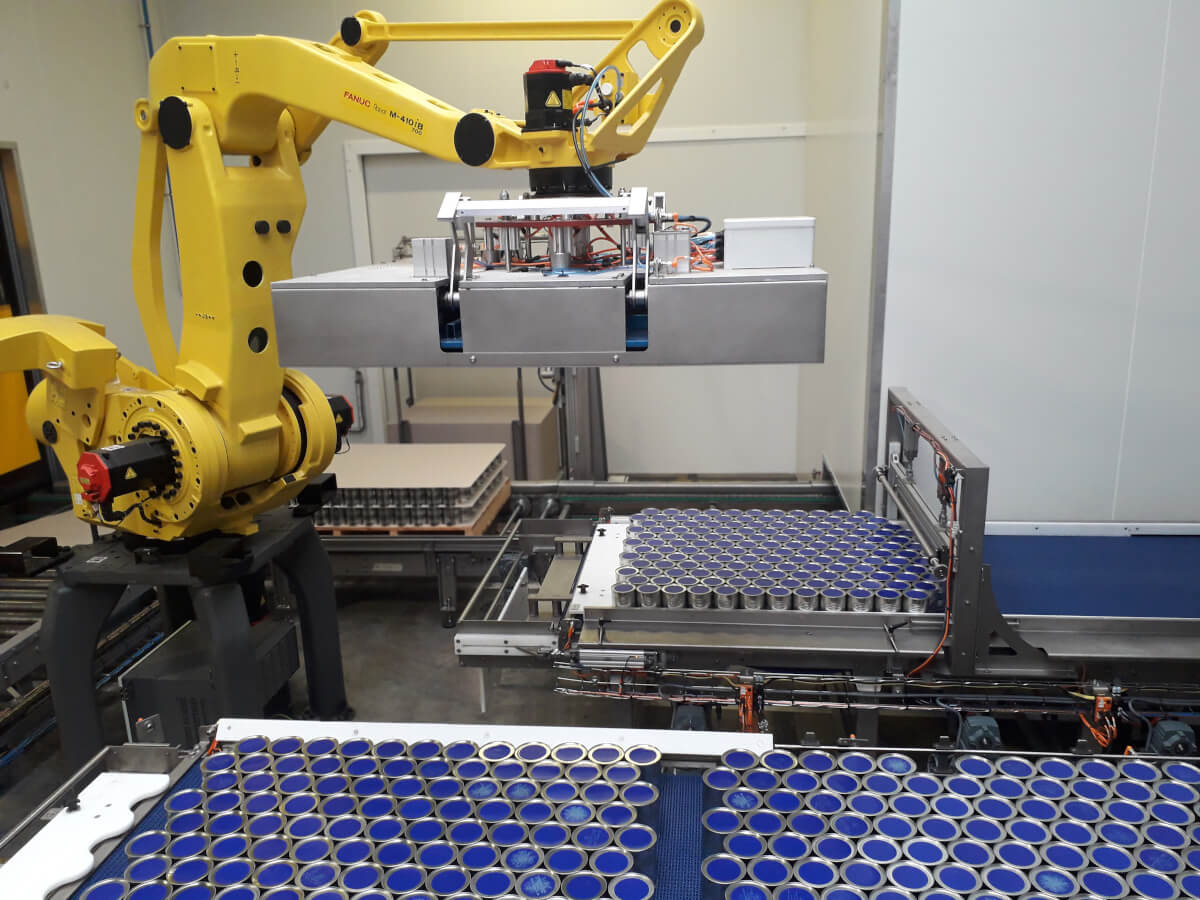
3. Buffer colis
Le buffer colis est une solution pour stocker, séquencer et alimenter des postes de palettisation.
Exemple de solution : Exotec, Miniload, Shuttle
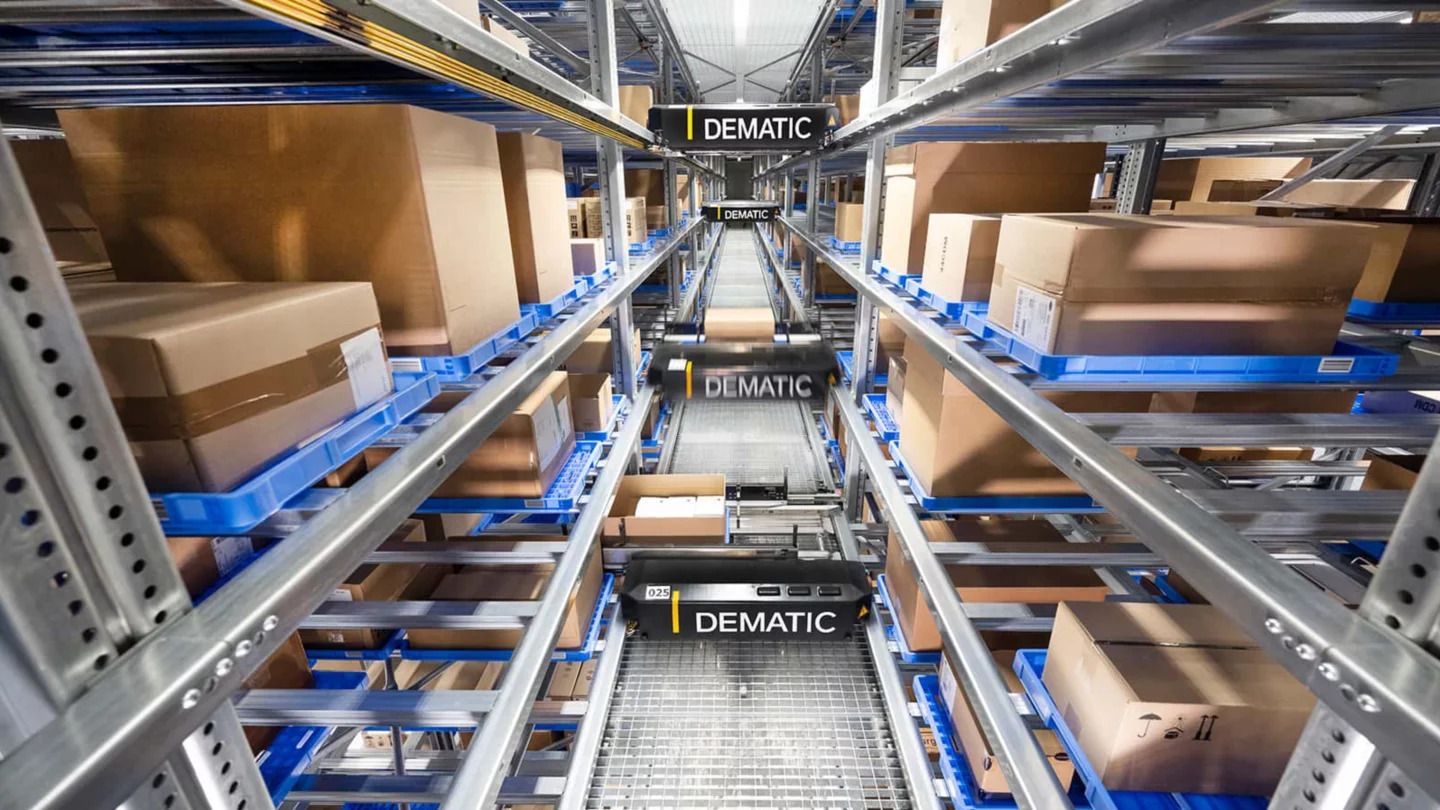
4. Palettisation
Deux types de solution existent pour la palettisation :
- Palettiseur automatique : ce système entièrement automatisé limite les OPEX, mais nécessite un système de calcul de palettes très pointu.
- Puits de palettisation : le poste de palettisation est conçu pour être ergonomique et faciliter la palettisation manuelle.
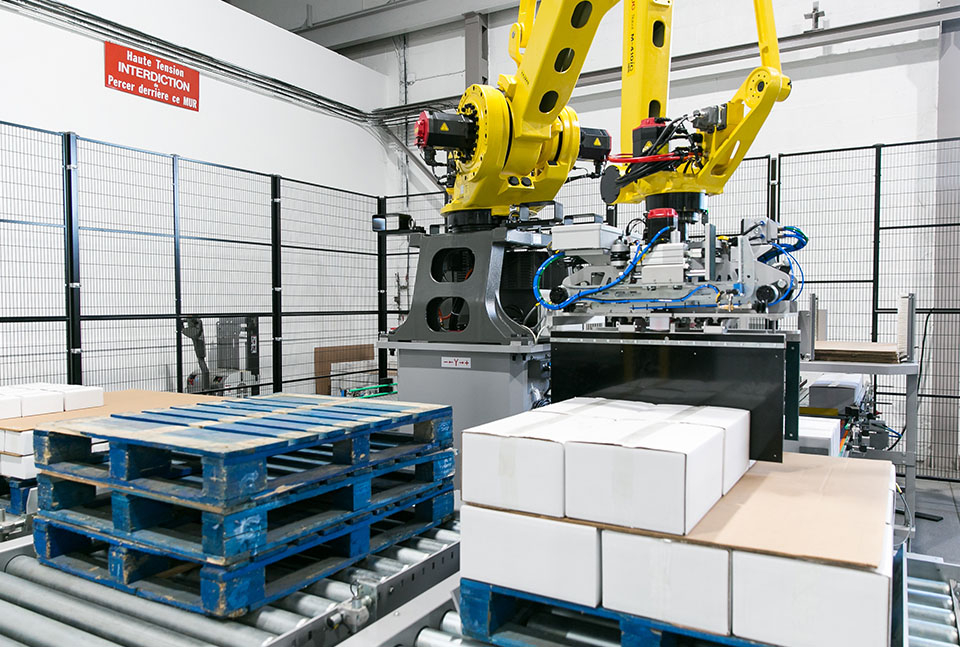
5. Expédition
Pour densifier, organiser et séquencer le chargement des camions, certains fournisseurs proposent un buffer d’expédition.
Exemple de solution : Transstockeur palettes, Shuttle palettes…
Les caristes récupèrent directement les palettes sur un gravitaire en face des quais et chargent les camions.
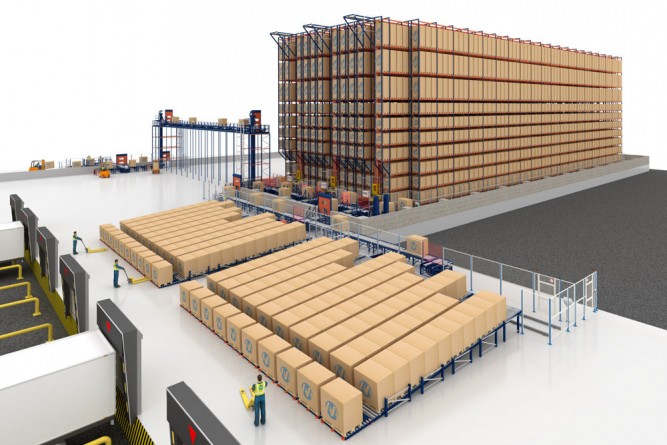
Les avantages de ce type de solution par rapport à un système de tri sont :
- La répartition des familles sur les palettes. Sur ce système, le tri en réception reste nécessaire pour la performance du système. Cependant, le buffer et le séquenceur laissent de la flexibilité. Deux "petites" familles de produits (en fonction de la taille du buffer) peuvent être injectées en parallèle tout en respectant la répartition sur les palettes clients.
- Adaptation du plan de palettisation en fonction des clients.
- En sortie de dépalettisation manuelle et automatique, un contrôle d'identification des produits est effectué (lecture caméra et contrôle de dimensions). Ces contrôles minimisent les erreurs en préparation.
- Cette solution est accompagnée d'un algorithme de palettisation. De nombreux critères sont pris en compte (famille, sous-famille, dimensions, poids, contenant...) pour assurer une palettisation "propre" et stable.
Cependant, cette solution de buffer nécessite 2 à 3 heures de dépalettisation avant de pouvoir lancer la palettisation. Ce décalage est à prendre en compte dans le dimensionnement de la solution.
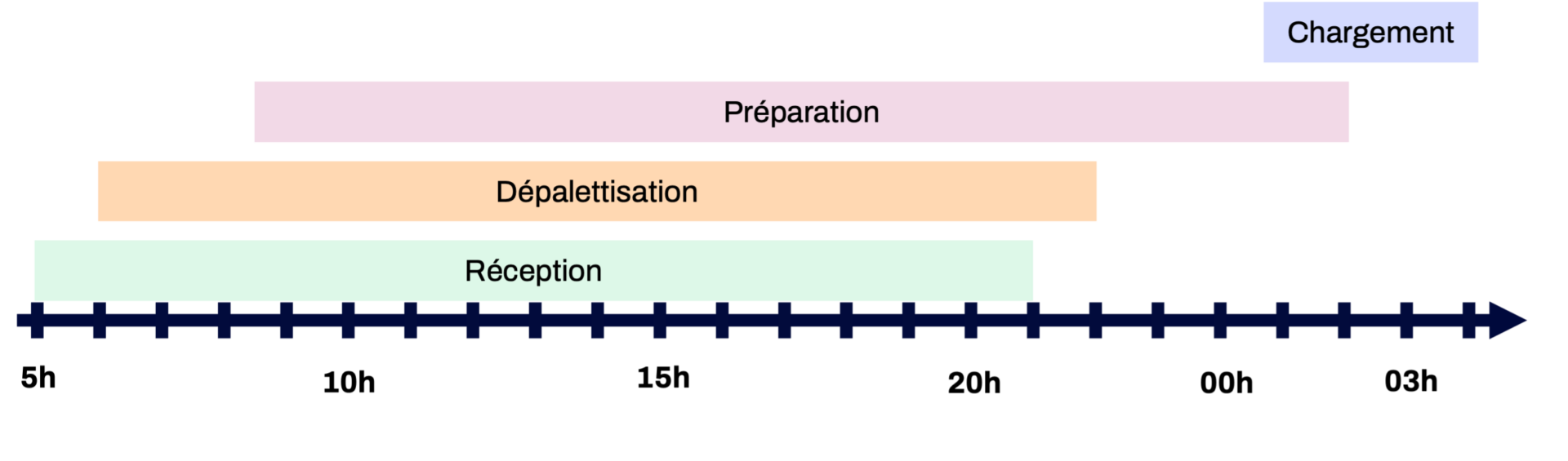
Il est possible de limiter ce décalage en jouant sur la réception et le traitement des offres et des familles. Par exemple, le flux sec qui n’a pas la contrainte d’être préparé dans la journée.
Centrale d'achats cliente
La dépalettisation automatique est essentielle pour garantir un fonctionnement efficace et rentable. Dans ce type d’entrepôt sans stock, les centrales passent des commandes à leurs fournisseurs identiques à celles reçues de leurs clients, mais les quantités ne correspondent pas toujours à des multiples de palettes ou de couches. Étant donné que la dépalettisation automatique nécessite des couches uniformes, il est recommandé de mener des analyses et de mettre en place des actions pour maximiser cette opération.
De plus, il est important de réaliser des études sur la qualité des produits reçus, notamment en ce qui concerne les étiquettes pour les lectures caméra, la qualité des palettes et l’absence de modifications d’emballage. Il est également nécessaire de sensibiliser les fournisseurs aux nouvelles contraintes du processus.
Fournisseur de la solution
Afin d’assurer une production ininterrompue, il est impératif de pouvoir palettiser en temps réel en fonction de l’arrivée des produits dans le système. Prévoir les palettes en début de journée en se basant sur les commandes des magasins n’est pas une option viable. Cette contrainte doit être prise en compte et intégrée dans le fonctionnement du système.
Avantages
- Qualité des préparations
- Qualité de la palettisation
- Flexibilité
- Réduction d'OPEX (dépenses d'exploitation)
- Pénibilité des manutentions limitée
Inconvénients
- Implantation longue (phase d'étude, montage, sensibilisation des fournisseurs)
- Investissement des équipes projets
- Fort investissement matériel
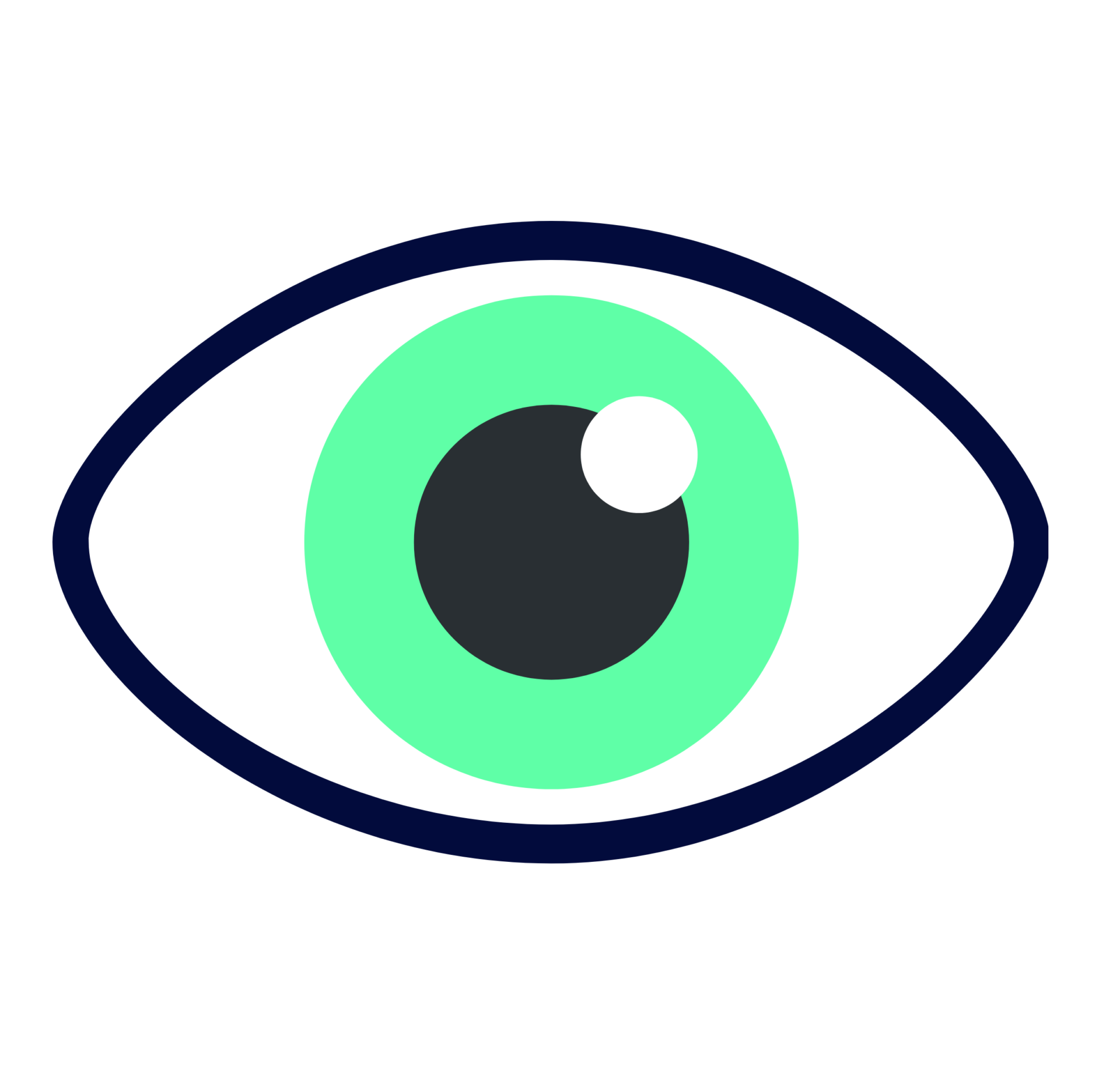
Bilan
La solution adaptée aux entrepôts dépend principalement des critères suivants :
- Disponibilité de la main-d'œuvre dans le bassin d'emplois
- Possibilité d'investissement
- Valeur perçue/quantifiée de la qualité par les clients (magasins)
- Délai d'implantation
Les fournisseurs de solution continuent à se développer :
- Pour diminuer la pénibilité, améliorer la productivité et raccourcir le Retour sur Investissement (ROI), les fournisseurs de trieur ont développé des solutions de dépalettisation automatique (remplaçant jusqu'à 3 postes manuels)
- Les premiers entrepôts frais entièrement automatisés ont été conçus avec un buffer sous technologie Miniload (mini-transstockeur). Plus récemment de nouveaux sites se sont construits avec une solution comprenant une technologie de type Shuttle. Cette technologie permet une grande flexibilité, un gain de productivité et une maintenance moins contraignante, mais pour un investissement plus important.
Une étude approfondie des données permet de valoriser ces différents scénarios pour éclairer les pistes d’évolution.